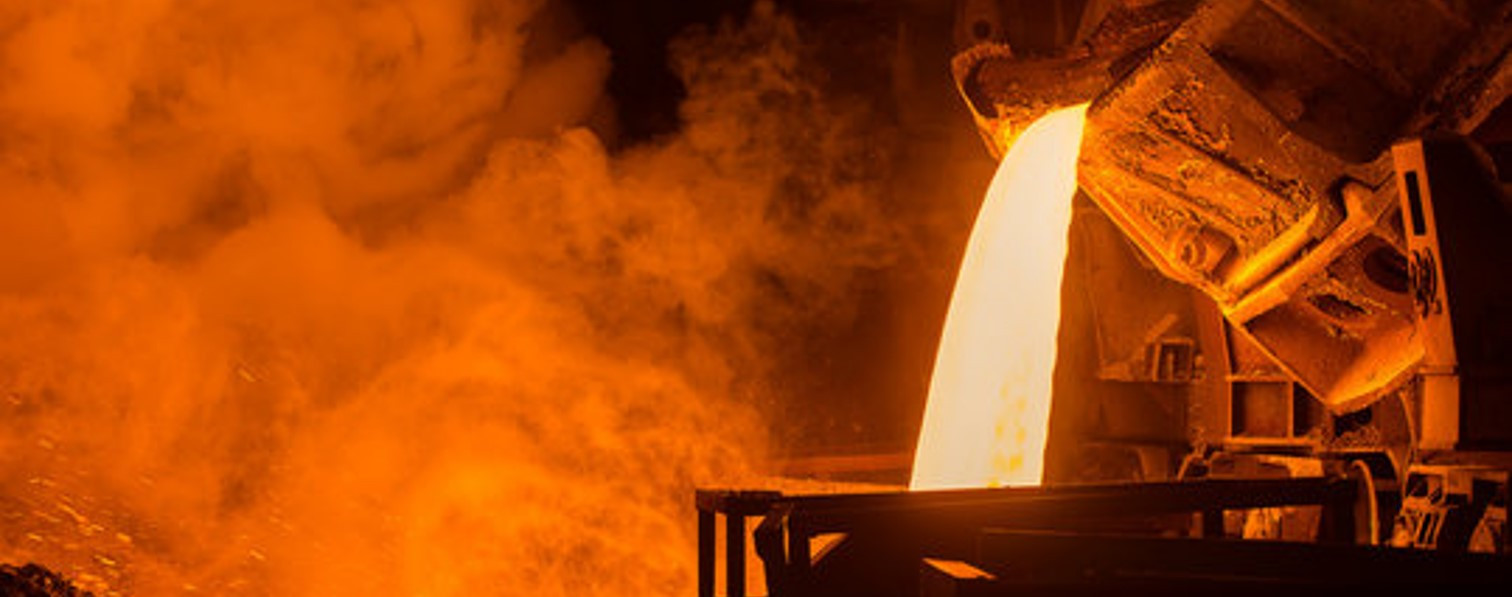
Green sand casting
Green-sand casting is made in a sand mold boned with clay to harden the sand. Sometimes, the hardening can be effects by mixing sodium silicate into the sand to create chemical bonds. The sand mold is used one time only.
The ejected casting will have a rough surface, low accuracy, and an excess material. The mold sand is suitable to be made big casting or low quality. This is the basic casting method and widely applied in the foundry companies. The advantages is the simple process, low investment cost, the machines and tools are very simple.
Furan casting
Furan casting is one kind of sand casting, using the mixture of furan resin and sand to create the mold for pouring process. Furan resin is commonly binder, self-harden material. Furan is mixed with sand then the mixture was shaped the desired mold, the flame burnt out the resin and the sand mold become solid, strong and unbreakable. The furan casting is popular in Japan companies. In this process, resin plays a very important role. The biggest advantage of furan technology is creating the casting with excellent surface, less defects and good dimension tolerance. However, the burning resin causes bad effect on environment.
Investment casting (lost wax casting)
Investment casting has been used in various forms for the last 5,000 years. The idea is creating the desired shape from wax, and the shell cover from suspension outside. After the cover is dried, it will be formed around the wax mold inside. The wax mold is heated and melted out of the outer shell cover. The space inside is mold cavity. The molten metal (aluminum, steel, cast iron, is poured into the mold cavity, the metal is gradually solid, and finally the shell cover is broken by vibration method. The excess of metal on casting surface will be remove by shotblasting. The final product will be checked the dimension, tolerance, and visual. The advantage of this technology is ability to make the highly dimensional product, exactly accurate and high quality and reduce machining process.
Some requirements of lost wax casting:
• The low melting temperature of wax (55-99⁰C) assures wax can melt out the shell.
• Durable wax sample is dimensionally stable under normal temperature.
• Good suspension
Lost foam casting
Lost-foam casting (LFC) is a type of evaporative-pattern casting process that is similar to investment casting except foam is used for the pattern instead of wax. Commonly cast metals include cast irons, nodular cast iron, steels, less frequently stainless steels and copper alloys are also cast. The size range is from 0.5 kg to several tons.
The first step of lost-foam casting is the creation of the foam mold. Next, the foam patterns are connect together as a cluster and the cluster is coated, also known as the refractory coating, via dipping, brushing, spraying or flow coating. After the foam mold is finished, it is buried in a container; for example, a metal drum; filled with compacted sand. The very ends of the foam shape are left exposed to facilitate the entry of the molten metal into the mold.
The benefit of lost foam casting is its ability to create casting with high dimensional accuracy, can limit the machining process. The excellent surface of casting as well as its exceptionally high dimensional accuracy are highly appreciated by the manufacturing companies.